Watch a 3D-Printed Handgun Fire 9 Rounds
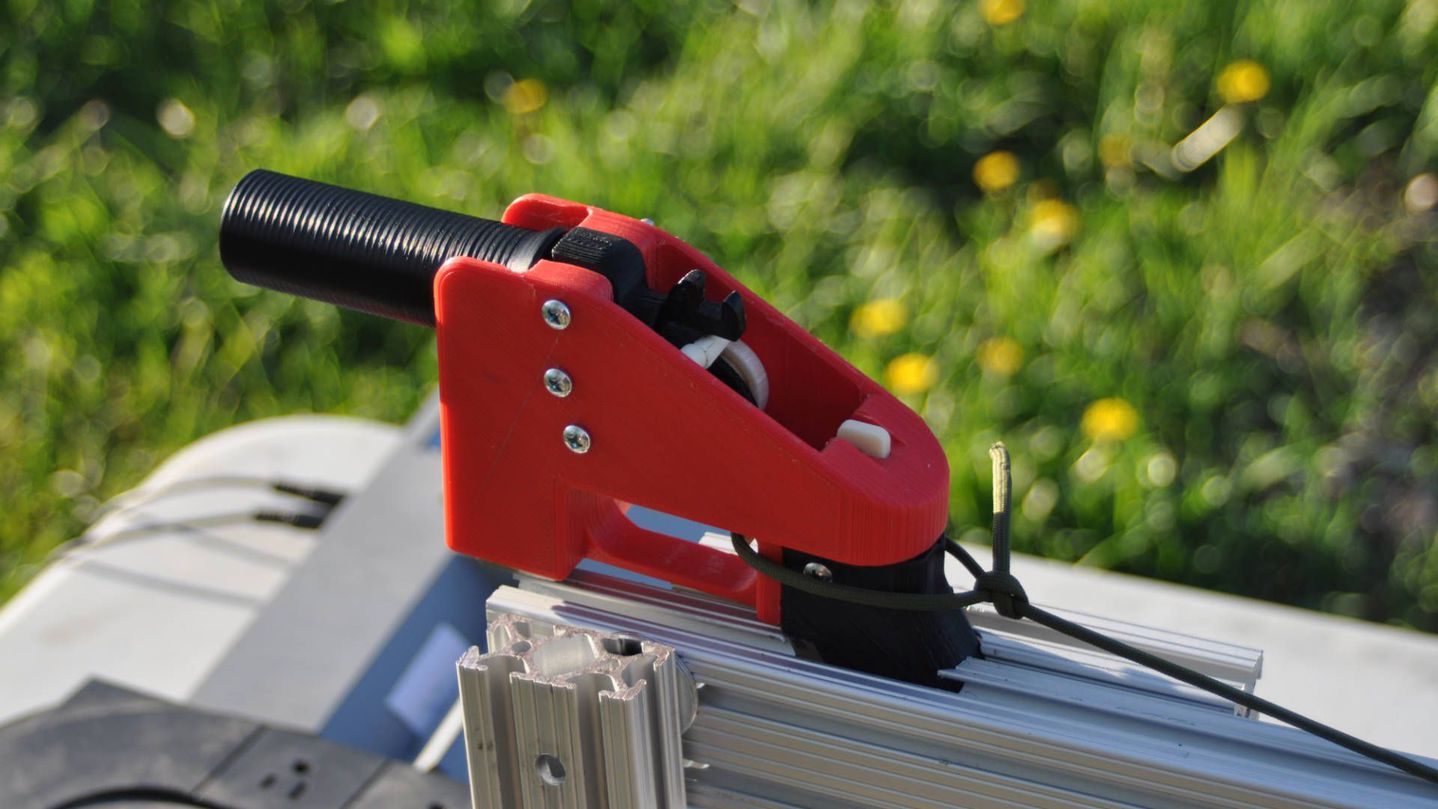
Just a couple of weeks after Cody Wilson and Defense Distributed released the files for the world’s first 3D-printed handgun, imitators have already replicated and improved upon it. Two gunsmiths from Wisconsin successfully fired their own Liberator nine times, without the gun showing any damage. As first reported by Forbes, two engineers, Michael Guslick and a man who refers to himself as “Joe” — he didn’t want to reveal his name — printed their version of the Liberator on a relatively cheap and unsophisticated 3D printer. Unlike Wilson, who used a $8,000 Stratasys, the Wisconsin duo used a consumer-grade $1,725 Lulzbot AO-101. They printed all the pieces within 48 hours and spent a paltry $25 in materials. “People think this takes an $8,000 machine and that it blows up on the first shot. I want to dispel that,” Joe told Forbes. “This does work, and I want that to be known.” As the video shows, the Lulz Liberator is functional — but making it so was trickier than it may appear. When the Guslick and Joe tested the “Lulz Liberator” last week, using .380 caliber rounds, the barrel snapped on the first try. But that barrel was actually printed on a Stratasys 3D printer owned by Guslick. He explained that the initial failure was “due to a compressed load and resulting cartridge overpressure.” Then the Wisconsin engineers used a barrel printed with Joe’s Lulzbot. The gun fired nine times over the course of the test — with its components remaining intact. The gun might have sustained even more shots, but the men decided to stop the test because of poor light conditions. Guslick, who was one of the first gunsmiths to experiment with 3D printing, wrote in an email to Mashable that it wasn’t easy to fire the handgun successfully. “The Liberator is actually a very finicky gun at this point,” he wrote. “We had many more times that it went ‘click’ rather than ‘bang.’” Guslick explained that for various reasons, the gun failed to fire with both barrels and even failed between successful shots. The main problem was the shape of the firing pin, which “appears to be crucial for operation,” he wrote. In fact, sometimes the firing pin wouldn’t hit the primer “dead-center,” and it required “several strikes” to ignite, Guslick wrote. Since Joe and Guslick didn’t use the firing pin retainer, a part of the original Liberator design, they lost a lot of firing pins and had to add replacements after each successful shot. The body screws bent from the recoil, which made more replacements necessary. Regardless, this is another step toward making functioning plastic guns more accessible to anybody with an Internet connection and a 3D printer, even a relatively cheap one. And it’s a step toward making those guns more efficient; maybe even deadlier. UPDATE, May 21, 11:50 a.m.: The story has been updated to clarify the issues that Guslick and Joe had with the firing pin. Images and video courtesy of Michael Guslick Read […]